6 Automation Innovations You Can’t Ignore in Manufacturing
_1737979167986-blog.png&w=3840&q=75)
Imagine a future where factories are more intelligent, efficient, and resilient. Thanks to a wave of automation innovations, this future is already here. Manufacturing is a fast-growing sector that is adopting automation across various stages of the process. Automation is revolutionizing the industry by reducing efficiency and operational costs and increasing productivity. From AI-powered robots to huge factories, from cloud-based analytics to AI and ML-powered forecasting, Manufacturing is on its way to fully automated.
Infosprint Technologies, a digital transformation company that provides industrial automation solutions, is a leader in manufacturing innovation. This blog will provide insights into six automation innovations redefining the landscape.
Industrial IoT (IIoT) for Smart Factories
The Industrial Internet of Things (IIoT) connects equipment, gadgets, and sensors to a central network, resulting in smart factories. This networked ecosystem allows producers to collect and analyze real-time data, improving decision-making and operational efficiency.
Predictive Maintenance
- Manufacturing automation tools analyze potential machine failures in advance. Therefore, companies can schedule maintenance proactively, minimizing unplanned downtime and productive disruptions.
- Machine care is typically less expensive than emergency repairs. It also extends the lifespan of the machines, reducing the cost of replacements.
- Predictive maintenance can identify potential safety hazards, such as overheating or excessive vibration, preventing accidents and injuries.
- It also enhances equipment performance and boosts overall productivity.
Improved quality control
- IIoT enables real-time data collection and analysis throughout the production process, allowing for immediate identification and correction of defects.
- Constant monitoring of equipment will ensure the product meets the highest quality standards.
- It will also reduce defects and improve customer satisfaction and brand loyalty.
- A strong focus on quality control enhances the company's reputation for producing reliable, high-quality products.
Energy efficiency
- IIoT systems can optimize energy usage by monitoring and analyzing energy consumption patterns across the factory floor.
- By optimizing energy usage, companies can significantly reduce their energy bills.
- Reduced energy consumption helps minimize the environmental impact of manufacturing operations.
- Optimized energy usage can improve overall operational efficiency and reduce operating costs.
- Shows a dedication to environmental sustainability and corporate social responsibility.
How do Collaborative robots and humans work together?
Collaborative robots, or cobots, are revolutionizing how manufacturing industries operate by working safely with humans. Unlike traditional robots, confined to a specific space due to their speed and potential risks, collaborative robots are built with safe mechanisms for human interactions. Due to their budgetary restraints on complex automation, collaborative robots are popular among small and medium-sized enterprises.
Increased productivity
- Cobots excel at handling repetitive and monotonous tasks like shipping, packaging, and quality checks.
- Workers can concentrate on more challenging tasks demanding creativity and problem-solving abilities.
- Businesses can enhance their operational efficiency by ensuring consistent performance and reducing errors.
- Production lines can operate longer with minimal downtime because cobots can work continuously without breaks.
Ease of integration
- Cobots often utilize drag-and-drop programming or no-code solutions, enabling non-technical personnel to program them with minimal training.
- Unlike traditional robots, which may take weeks or months to configure, cobots can be deployed in days or even hours, depending on the complexity of the task.
- They are lightweight and portable, enabling them to move between workstations and perform various functions.
Safety
- Cobots are equipped with safety sensors, cameras, and force-limiting technology to ensure safe interactions with humans.
- They are designed to detect nearby humans and halt their movements to prevent accidents.
- These are programmed to operate under speed limits and with restricted force, ensuring that injuries remain minimal in case of an accident.
- Advanced cobots use vision systems or proximity sensors to anticipate movements and maintain safe distances from humans.
Artificial Intelligence and Machine Learning in Manufacturing
AI and ML are transforming manufacturing by introducing intelligent, data-driven automation and process optimization capabilities. Automation software for manufacturing allows machines to learn from prior data, adapt to changing conditions, and continuously improve their performance.
Enhanced Process Automation
- AI algorithms analyze the workflows for bottlenecks, redundancies, and opportunities to optimize production speed and reduce downtime.
- It can monitor the machine's performance, predict when it might fail, and schedule maintenance.
- AI-powered robots can do operations like assembling, welding, and material handling more precisely and quickly, minimizing the need for human interaction.
Demand forecasting
- Machine learning algorithms analyze vast data sets of past sales records, machine types, market trends, and external factors like weather to predict future trends and market demands.
- Manufacturers can schedule production needs based on market research, ensuring they avoid both overproduction and underproduction.
- It also helps inventory management by suggesting materials needed based on market demand, reducing excess stock and stockouts.
Defect detection
- AI and computer vision cameras can evaluate items during manufacturing, detecting surface flaws, measurement errors, and color mismatches in real-time.
- ML models are trained on defective data sets, enabling them to recognize subtle changes.
- As AI systems are analyzed frequently, they will more accurately identify defects.
- Early detection can prevent the products from moving forward in the production line, reducing time and cost spent on rework and returns.
Meet Your New Co-workers: Intelligent and Efficient AMRs
Autonomous Mobile Robots (AMRs) are revolutionizing material handling and logistics in production by offering more innovative and more adaptive solutions than traditional Automated Guided Vehicles (AGVs). Unlike AGVs, which follow predefined tracks or fixed routes, AMRs utilize advanced technologies such as sensors, cameras, and artificial intelligence to navigate dynamically. This capability makes them more adaptable and efficient in modern manufacturing environments.
Flexibility
- AMRs use technologies such as LiDAR, cameras, and simultaneous location and mapping to create a real-time map of their surroundings, enabling them to navigate and detect obstacles.
- They are infrastructure-free, making them ideal for facilities with frequently changing floor layouts.
- Simultaneously, they can modify their real-time routes to bypass traffic in congested areas or identify the most efficient path to their destination.
Cost-effectiveness
- AMRs can reduce operational costs and automate labor-intensive tasks, such as moving materials, finished goods, and waste between workstations, freeing workers for high-value tasks.
- Since they operate independently, they don't require considerable maintenance.
- They are equipped with energy-efficient batteries to work for extended periods with minimal recharging downtime.
Scalability
- AMRs can be quickly programmed and deployed without extensive installation processes.
- Adding new robots to the fleet is straightforward and doesn’t require significant facility reconfiguration.
- Advanced software enables multiple AMRs to work together, distributing tasks intelligently and ensuring optimal resource utilization.
- To ensure cost efficiency, manufacturers can increase the number of AMRs during peak production periods and reduce them during low-demand times.
How are digital twins transforming the manufacturing industry?
A digital twin creates an electronic version of a real-world item Process or system process or system. By modeling real-world activities, digital twins allow firms to test scenarios, optimize procedures, and forecast outcomes without disturbing production.
Proactive problem solving
- Digital twins collect data from sensors on machines and equipment, providing a real-time view of operations.
- AI and machine learning power this; they can predict potential issues, such as equipment failures, and suggest corrective actions before they happen.
Process optimization
- Manufacturers can test various production scenarios, such as increasing machine speed or altering material inputs, without impacting the physical production line.
- Digital twins enable manufacturers to optimize layouts, resource allocation, and equipment utilization by simulating the effects of changes on production.
- Analyzing energy consumption data can suggest adjustments to reduce waste and improve sustainability.
Training and simulations
- Virtual simulations allow employees to work with machinery, gaining hands-on experience without disrupting production or risking safety.
- Before changing the machine parts or modifying the equipment, they can use digital twins to monitor the performance of the parts before making actual changes for smoother transitions.
- Digital twins can model emergency scenarios, including equipment failures or supply chain disruptions, allowing personnel to train and prepare for unexpected events.
Hyper Automation
Hyperautomation automates complicated processes from start to finish using a combination of technologies such as UIPATH RPA (Robotic Process Automation), AI, and machine learning. This strategy ensures that human tasks and automated technologies work together seamlessly.
Increased efficiency
- Hyperautomation integrates various automation technologies like RPA and IoT in the manufacturing lifecycle for a seamless production process.
- It reduces manual intervention by monitoring machines, inventory management, and quality inspections.
- Automated systems work 24/7 without a break, ensuring a faster production cycle and efficient meeting of demands.
Enhanced decision making
- Hyper-automation can analyze data in real-time by continuously collecting data from IoT sensors, providing insights into production performance and machine health.
- Insights generated by hyper-automation solutions help manufacturers allocate resources like labor, materials, and energy more effectively, reducing waste and maximizing output.
Scalability
- Hyperautomation systems can be used in various departments and operations, including production, logistics, customer support, and sales.
- Manufacturers may control operations across numerous sites from a single interface by integrating machines, systems, and facilities via IoT and cloud-based platforms.
- As businesses grow, hyper-automation technologies can readily accommodate higher production volumes, new product lines, or extra facilities.
Why Manufacturing Innovations Matter
The manufacturing sector faces ongoing pressure to enhance efficiency, reduce costs, and maintain quality while adapting to changing customer demands. Innovations in automation, such as IIoT, cobots, AI, AMRs, digital twins, and hyper-automation, enable manufacturers to tackle these challenges effectively.
Neglecting these advancements can result in falling behind in a highly competitive industry. Manufacturers who adopt these innovations will improve their operations and set themselves up for long-term success. As automation technologies continue to develop, staying ahead of the curve will be essential to achieving operational excellence in the manufacturing sector.
Related Reads for You
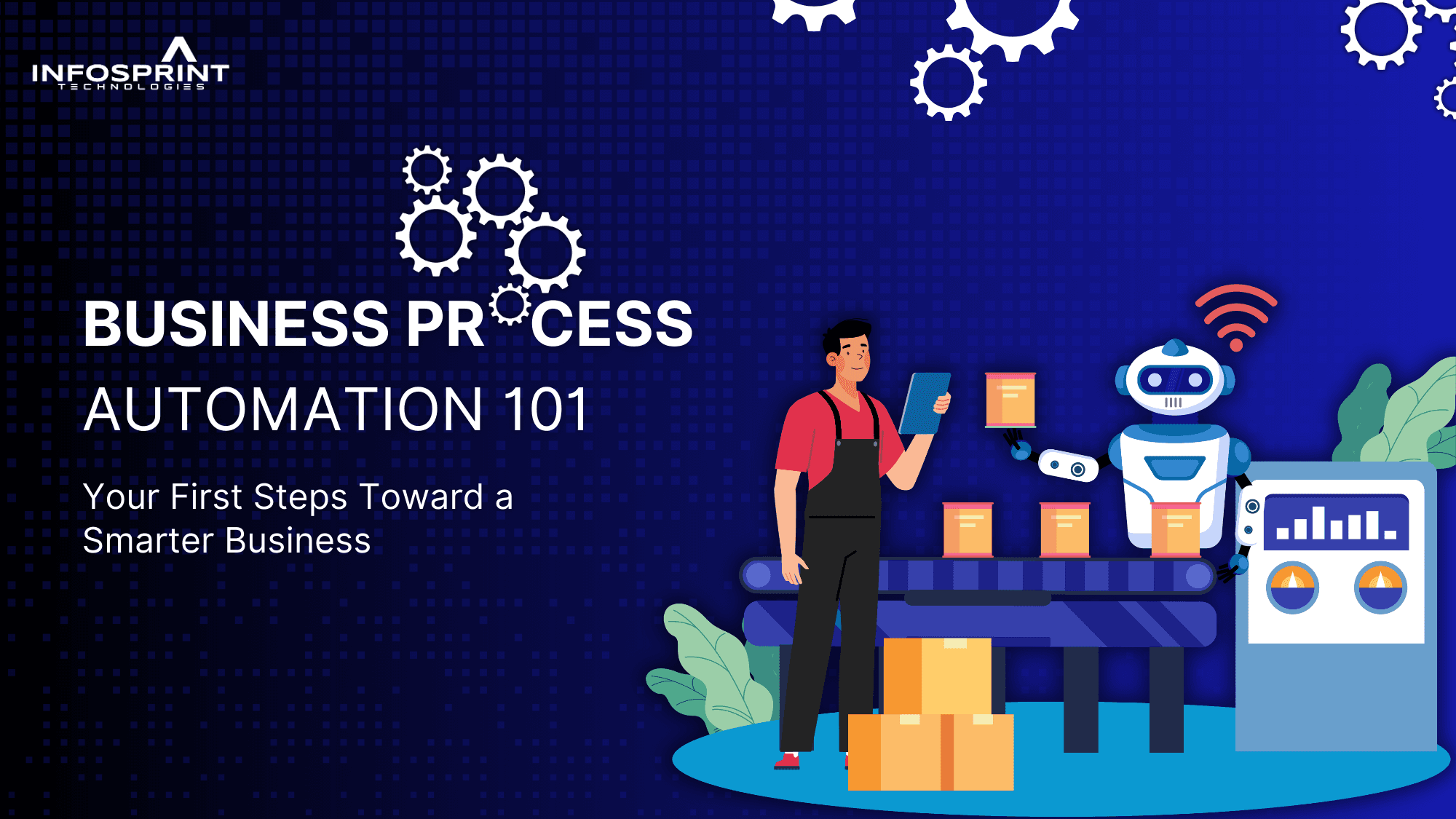
automation
Business Process Automation 101:...
Discover essential steps and best practices for successful business process...
_1734349887090-blog.png&w=3840&q=75)
automation
2024 Most Influential Automation...
Discover the top automation technologies shaping 2024. Explore how these...
_1738653793705-blog.png&w=3840&q=75)
automation
Salesforce Agentforce vs Traditional...
Enhance customer service with Salesforce Agentforce, an AI-powered Salesforce cloud...